Experiment: Bevel "Polishing"
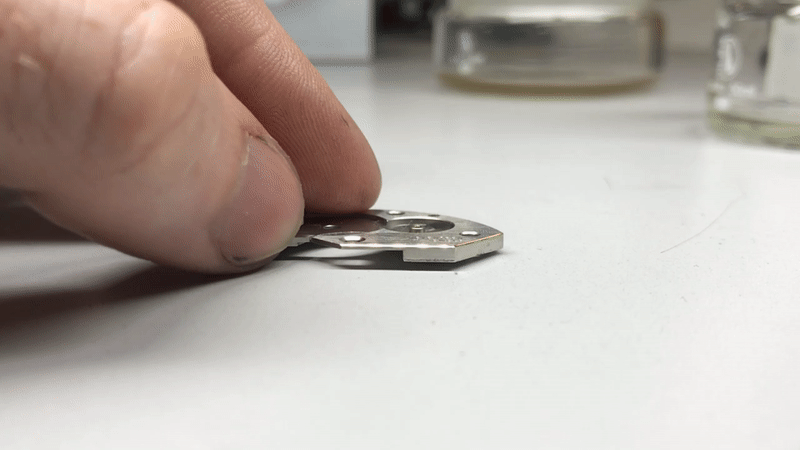
Most high-end watches' bevels are hand-polished [citation needed], and it's incredibly difficult to achieve that level of polish... But I gave it my best shot anyway.
The Geneva striping on my school watch was slightly delayed, long enough to let me consider just how much difficult it would be to polish my bevels.
The answer: very hard to impossible.
Polishing is a tricky word, because for most people it just means "shiny." For watchmakers, it means "perfectly texture-free at the lowest power magnification, usually 3x." There's a lot of air between those definitions.
"Polishing" and polishing tools. The steel tool burnishes, while the pegwood uses diamond paste to do the real deal.
My previous bevels were finished with 9 micron lapping film, which gave them a pleasing gleam, but no shine. To properly shine, the bevels must be polished (to watchmaking standards), and that's only done with diamonds.
To be properly polished, a bevel must be formed and lapped as finely as possible (we go down to 0.5 μm lapping film), and then polished with diamond paste. It's critical for the bevel to be completely flat, otherwise the lapping process will reveal all sorts of structural issues, and the polishing process will take forever.
Hand polishing this way is extremely difficult. The bevels get nice and shiny, but under magnification it's possible to see light scratches from the diamond paste, and thus doesn't qualify as true polishing. Brass is soft and scratches easily, so these marks are unavoidable. Or are they?
Enter the burnisher. Previously used to fix plexi crystals and dials, it can also work magic on bevels. After being thoroughly lapped, the tool can take bevels to a near-polished state by burnishing the metal—with the added bonus of flattening the bevel out, since the geometry of the edge is slightly convex, and will ride smoothly on the high point of the rounded curve, if used properly.
Still, that's not polished. For a true polish, we need speed and heat. Enter the rotary tool (popularly known as a Dremel).
Charged here with luster paste from our case refinishing supply.
This felt wheel may be small, but at 25,000 RPM, it generates some serious heat. Just as with polishing cases, the bevel has to be held at precisely the right angle, and due to the softness of my (cheap) felt wheel, I had to use almost no pressure. That said...
That's polished.
From any angle, it's a smooth, mirrored surface. Amazingly, the felt wheel didn't ruin my geometry or angles, and I was actually able to keep things flat and square. Still, holding a Harbor Freight rotary tool to my bridges at 25,000 RPM is a harrowing proposition, so I decided on a more gentle approach.
Not polished, but finer than a line finish. Let's call it a "shine" finish.
The end result is in the no-man's land between line finishes and polishing. In other words, it would be unacceptable in the real world, but it's probably OK for a first-year watchmaking student.
I lapped down my bevels to 0.5 μm, burnished them and smoothed out the finish with the diamond paste. It's not quite as flawless as the rotary tool's polish, but it's pretty close.
I'm not sure how the rotary tool would treat my bridges, so I'm content to live with this finish for now. It's imperfect to those in the know, but it catches the light and glitters almost as well as the real thing.
The bevels will stand out nicely against the Geneva striping on the tops of the bridges.
As pretty as it may be, it could still improve—and as George Daniels once quipped, a watchmaker turns to finishing when they run out of technical talent. I don't know that I agree, but I'm happy to let my bevels stand at their current position... At least, as long as I'm not able to mull my options for too much longer!
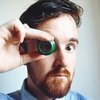
Watchmaking student at the Lititz Watch Technicum, formerly a radio and TV newswriter in Chicago.