School Watch: Beveling
One of the things that separates ordinary watches from truly high-end ones is the finishing involved. Hand-finishing is an art of its own, and we're getting a taste for it with our school watch.
The bevels on any component are a sign of the care put into its manufacture. Bevels not only provide the necessary deburring of hard edges that machining requires, but they also indicate the level of craftsmanship involved with the part's production.
The bevels on our school watch are cut by hand, with some minor exceptions that I'll cover later. The usual tools to cut bevels on watch bridges are very fine files or abrasives, though I also found success using a graver to lightly and carefully scrape material away.
Using the graver isn't exactly classic watchmaking, and it carries a heavy risk of damaging the workpiece—it's sharp, hardened steel, and it'll gouge the brass without even trying! I wouldn't recommend it to others, but it fit well with my working style.
The requirements for bevels are simple, yet maddeningly difficult to achieve:
- All bevels must be the same width, both within a single bridge and between bridges.
- Bevels must be a consistent width for their length, without wide or narrow sections (this is especially tricky at the ends).
- They must be flat and at a 45° angle to the sides and top of the bridge.
- The surface finish must be smooth and even, whether polished or left with a line finish. Any other texture must be removed.
- All corners must meet sharply, with a defined border between them.
That's it! Try not to lose your mind in the process.
Keeping everything evenly-sized on one bridge is tricky enough, but matching the bevel size between bridges is downright difficult. It requires a dispassionate eye and an objective view of the project to pull off—otherwise, magical thinking can trick you into seeing things that aren't there.
Flatness is another constant struggle. Bevels are generally fairly small, and it's very easy to rock your tool slightly while cutting them. Rolling the piece around in the light will reveal how flat you've kept things, since reflections on rounded bevels will be thin and inconsistent, while flat bevels will reflect evenly along their length.
Corners are another trap. Slipping with your tool will clip the sharp edge, rounding the border and requiring you to expand the bevels to reëstablish it. Of course, since all bevels must be the same size, enlarging two means enlarging a dozen others. It can become a rabbit hole extremely quickly. This border took me hours to properly form; the meeting of three bevels creates this Y-shaped corner, adding a third dimension to an already difficult operation.
There is a shortcut to all of this, and that involves the lathe again. Centering on a recess and manually rotating the headstock, like on the bridge shaping, can crisply quickly cut a perfectly flat, polished bevel, and the border between them will be razor-sharp as seen above. The click, ratchet wheel and crown wheel recesses were all done this way, both for time's sake (we have deadlines to hit!) and because the short recess height makes it extremely difficult to access with a hand tool.
I finished my bevels with 9μm lapping film, which leaves a satin line finish. They shine, but don't glint. I may decide to go back and polish them before the final surface finish is applied to my bridges, but that is a trap as well—the finer the surface finish, the more you can see texture and flaws in the bevels.
They could use perfection, but I'm satisfied with my work for now. This is just my first attempt at beveling bridges, and I'm trying to keep my expectations grounded in reality. There will be many more opportunities to keep honing this skill in the future.
Next up, the final surface finish. That's another unique skill, and will make the watch extremely delicate to handle. Coming soon!
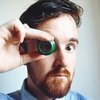
Watchmaking student at the Lititz Watch Technicum, formerly a radio and TV newswriter in Chicago.