Tooth Profiles
Most machining uses a single gear tooth profile, but watchmaking strikes off on its own path.
Involute gearing, via wikipedia.org/Claudio Rocchini
Gears with straight teeth have tons of sliding friction, making them awfully inefficient. Modern machines use involute gearing, which use teeth cut on the involutes of a circle, making the contact a rolling action which reduces friction and lowers stresses on the entire setup.
Watches, instead, traditionally use cycloidal gearing, which has a similar rolling action, but with a different kind of tooth profile. Cycloidal gears have a distinct contact at the pitch circle (the round bit near the middle), with a tapered addendum (the tip above the pitch circle), and a dedendum (the rest of the tooth below the contact point).
Cycloidal gears run with very little friction, making them perfect for low torque machines like watches and clocks. Unfortunately, the fact that they have such a small rolling friction area means that they're also very susceptible to depthing errors, so their pivots have to be precisely located in order for the mechanism to function properly.
The design of cycloidal gears means that the teeth will necessarily have some space between them, which is usually fine, but can cause problems with the second hand "juddering" as the hand wiggles within the empty space between teeth. The classic solution to reduce the second hand's judder was to add a friction spring to the seconds pinion, holding the pinion steady, as seen above, but they can be easily bent and malfunction. For a better solution, watch manufacturers now use a new profile that's typically called "microgearing" to eliminate the lash.
Microgears have a fuller, thicker tooth profile, which allows significantly less free space between the teeth than cycloidal gears. You can see in the photo above how the wheel's tooth almost completely fills the space between the pinion leaves.
Many manufacturers now use a blend of both profiles, depending on the need of that particular geartrain. Above, you can see that the counting train (from the barrel to the escapement) is cut with microgears to minimize judder in the sweep second hand, while the ratchet wheel still uses traditional cycloidal gears for maximum smoothness and efficient power transfer.
A third tooth profile also exists, but is typically only found in chronographs. Triangular teeth have very poor frictional characteristics compared to cycloidal teeth, but they are very good at coming in to and out of engagement with each other without binding. In a classic horizontal clutch chronograph like the Lemania 1873, the clutch wheel (top) stays in engagement with the driving wheel (left), but pivots to engage or disengage with the chronograph wheel (right). Since the driving wheel and clutch wheel are always moving, it would be possible for the clutch and chronograph wheels to be aligned tip-to-tip at certain points, which could jam if both wheels had blunt cycloidal teeth. Triangular teeth, with their sharp tips, will (almost) invariably mesh perfectly, regardless of their alignment.
As with all watchmaking, nothing is a hard rule, and many modern chronographs use microgearing on their chronograph and clutch wheels, like the ETA 7750.
There are certainly other wheel profiles that I've missed—and I don't pretend to be an expert on any of this—but I think it's interesting and worth pointing out. Any gearing experts are very welcome to chime in and set me straight on any of this!
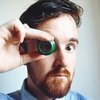
Watchmaking student at the Lititz Watch Technicum, formerly a radio and TV newswriter in Chicago.